Mixer-Cooker
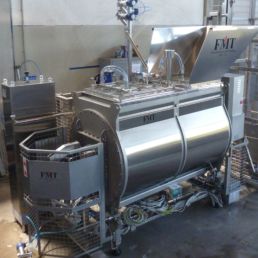
Correct preparation of the batch is essential to obtain a high quality end product.
FMT Mixers / Cookers are designed and created for homogenous batch processing with particular attention to the processing of various ingredients that can make up a recipe.
The Mixers / Cookers can be incorporated with various automation systems to facilitate and industrialise the various operations and are designed to process products with or without pieces.
The FMT Mixers / Cookers have the essential feature: the internal batch stirring system is also the thermal transfer component.
With this technological innovation, FMT has eliminated the static and hot parts in contact with the product, thus eliminating the risk of “burning” of part of the batch.
The automation systems available are:
- Load cells
- Trolley elevator
- Flow meters
- Worm screw for powder products
- CM 1000 (for 1000 L batch)
- CM 1500 (for 1500 L batch)
- CM 2000 (for 2000 L batch)
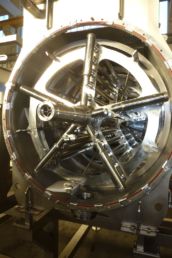
Capping machine
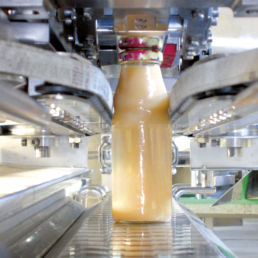
The FMT capping machines, entirely manufactured in stainless steel, are designed to permit the closing with or without steam of glass bottles and jars, through different types of caps.
The consolidated reliability, the easy format change and the high levels of vacuum and hygiene achieved, make these machines particularly suitable for the canned food and beverage sectors.
Thanks to the flexibility and modularity of their range, FMT Capping machines can be used both in low speed and high speed lines (up to 800 cpm).
Based on the different needs, in terms of production capacity and autonomy, different feeding models can be supplied with the machines.
CAPS FEEDERS
The FMT feeders allow the automatic and uniform feeding of caps, from the loading hopper to the capping machine, orienting them correctly.
Depending on the speeds and on the required autonomy, various models make up the range of FMT caps feeders, with a production range reaching up to 900 cpm.
Since the FMT feeders can be installed in a close or remote position with respect to the Capping machines, they are proposed and designed according to the available spaces and to the specifications of each project.
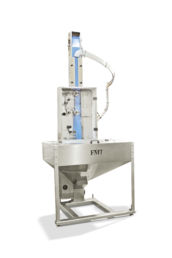
The Twist Off Capping machines can be found in four versions:
Depalletisers
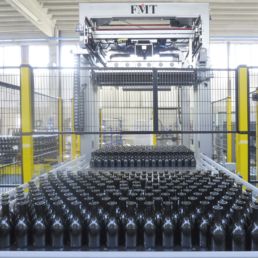
FMT has developed its range of automatic depalletisers with particular attention to flexibility, in order to be able to process different types of containers with the same machine.
Thanks to the development by “blocks”, each Customer can personalize the machine in relation to the degree of required automation.
In fact, the FMT Depalletisers can be composed starting from a semi-automatic machine up to a “full optional” model, with a maximum degree of automation and autonomy even at high line speeds (up to 1.000 cpm)
Special attention to the choice of high quality materials and a sturdy structure are the key elements of this FMT product range, that make it possible for us to ensure high performance levels over the years.
The different Depalletiser models can be equipped with:
- Automatic system for the withdrawal of layer pads
- Automatic pallet feeding and unloading system
- Buffer belt conveyor and alignment system, on a single row, for containers outfeed
- Low level - GEMINI Model.
- High level - ATHENA Model
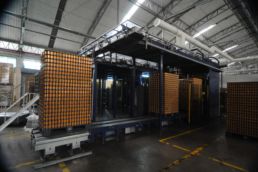
Traditional Palletisers

FMT has developed its range of automatic palletisers for processing cartons, shrink-wrapped packs and trays.
The product can be fed from above or below
The palletiser can also be of the Multiliner type, capable of processing simultaneously two or more types of differently sized packages and capable of palletising them separately
Special attention to the choice of high quality materials and a sturdy structure are the key elements of this FMT product range that make it possible for us to ensure high performance levels over the years.
The different palletiser models can be equipped with:
- Automatic layer pad deposit system
- Pallet destacker storage unit
- Integration with automatic pallet winder
The palletisers can have two configurations
Storage Systems / Conveyors
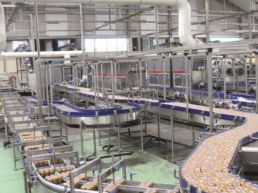
As a supplier of complete lines, over the years FMT has developed several containers handling systems to meet the needs of its Customers.
In fact, in order to have lines with high production efficiency, it is essential to have conveyors and storage systems with high quality and advanced technology.
Behind each line, there is a very important engineering design that uses all available handling technologies to be able to develop the best final solution for each project.
Among the various FMT systems to complete its lines, we have:
- Belt conveyors
- Elevators / lowering devices for cartons or single containers
- Drying tunnel
- Empty or full containers washing machines
- Buffer (FIFO or LIFO)
- Containers overturning machines
- Tilting conveyors for cap sterilisation (Hot Fill)
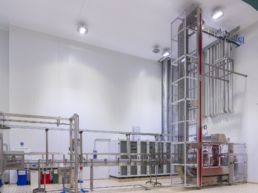
Palletiser / Depalletiser
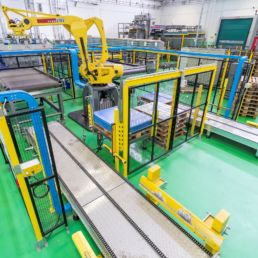
Robotic palletising and depalletising system for unpacked containers.
The system is designed and studied to receive containers from the filling line, place them on pallets which will then be placed in quarantine or in storage units to be labelled at a later date
Subsequently, the pallets return to the Robot, which will depalletise the containers and send them to the secondary packaging line.
The system is tailor-made and gives the possibility of making maximum use of space available.
The possible coupling with suction cup pick-up systems and arms on the heads enables the combined pick-up of empty layer pads and empty pallets.
The technology of palletising and depalletising with robot was developed for both medium and high speeds.
The palletising and depalletising system with Robot has different customisation options. Its main feature is flexibility, as it is a technology that can be configured based on specific Customer’s requests:
- Possibility of managing both the palletising and depalletising functions with a single Robot.
- Various types of heads to be chosen according to the type of container, such as: metal cans, glass bottles and jars
- Very fast format change
- Expandable for increased production
- High residual value of the robot over time
- Reduced maintenance costs
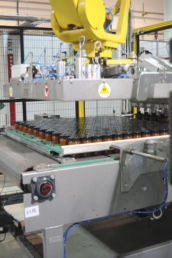
Robot Palletisers
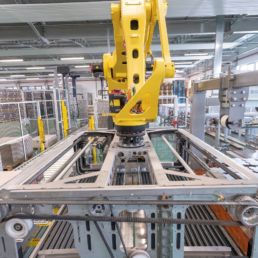
The ZEUS Robotic palletising systems are developed to meet the most modern needs of the food industry. Thanks to a wide variety of special multifunction heads, they are able to meet the packaging needs of most containers and packages.
In particular, they represent an alternative to traditional palletising systems.
The possible coupling with suction cup pick-up systems and arms on the heads enables the combined pick-up of empty layer pads and pallets.
The ZEUS Robotic palletising has been developed for both low speed and high speed.
SPEED from 3 to 120 ppm
(*) The speed depends on the size of the package and the palletising layout.
The Palletising system with Robot has different customisation options. Its main feature is flexibility, as it is a technology that can be configured based on the specific customer requests:
- Possibility of palletising several lines simultaneously
- Ability to palletise packages of different size and type simultaneously
- In most cases, format change without the need for mechanical intervention. Carried out by program insertion or selection
- Limited installation space
- Expandable for increased production
- Reliability, flexibility and possibility to reconvert the system
- High residual value of the robot over time
- Pick-up head with suction cups
- Pick-up head with pneumatic or motorised grippers
- Pick-up head with rack
- Magnetic pick-up head
- Basket pick-up head
- etc....
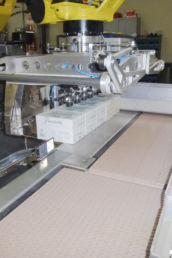
Palletizer configurations:
Horizontal Tunnels
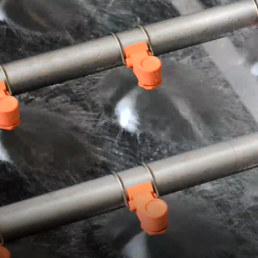
HORIZONTAL TUNNEL FOR PRODUCT THERMAL TREATMENT
It is a modular range of Tunnels for pasteurising, warming and cooling food products inside different types of container: cans, glass bottles and jars, plastic bottles.
The modular belt conveyor system ensures a
significant product stability, making operation extremely simple and reducing significantly maintenance.
The product can be handled on one or two stacked levels.
The simple operation and maintenance as well as the quality of the treatment performed, make the FMT Tunnels ideal machines for the pasteurising, warming and cooling cycles of all types of contain
An extremely flexible and innovative work platform, designed to meet the pasteurisation needs of the most demanding Customers.
Advanced technological solutions that enable FMT to manufacture machines at the highest levels available on the market today.
- Fast and accurate thermal treatment
- Maximum care for the most delicate products
- Modular configuration
- Energy saving systems
- Pasteurisation Tunnel
- Calorie recovery Pasteurisation Tunnel
- Heating Tunnel
- Cooling Tunnel
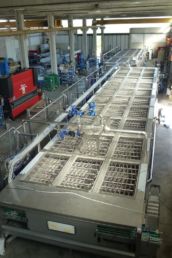
The various technologies of horizontal tunnels can be found in four machine versions:
Piston fillers
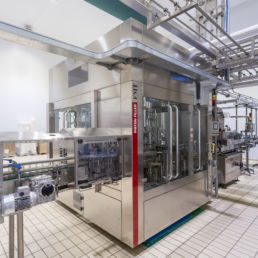
This technology is ideal for filling any type of viscous or dense product, with or without pieces such as, for example, marmalades, sauces, ketchup, mayonnaise, pât, baby food, honey, spreads.
Using a mechanical technology for the filling, the Piston filler also has the advantage of being very robust and easy to use equipment for operators.
It is extremely flexible and can be adapted to the filling of different types of products
- Standard valve or “rotary” valve.
- Valve with Horizontal or vertical plungers.
- Valve with membrane.
It is available both in the linear version, for low speeds, and in the rotary version for medium-high speeds.
- Filling from the bottom
- Automatic piston extraction system for CIP
- Customised nozzles in relation to the product
- Conical or cylindrical valves or with membrane
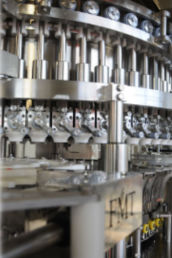
The various technologies of the piston filler can be found in four machine versions: